The Importance of Regular Maintenance for Industrial Equipment
The Importance of Regular Maintenance for Industrial Equipment
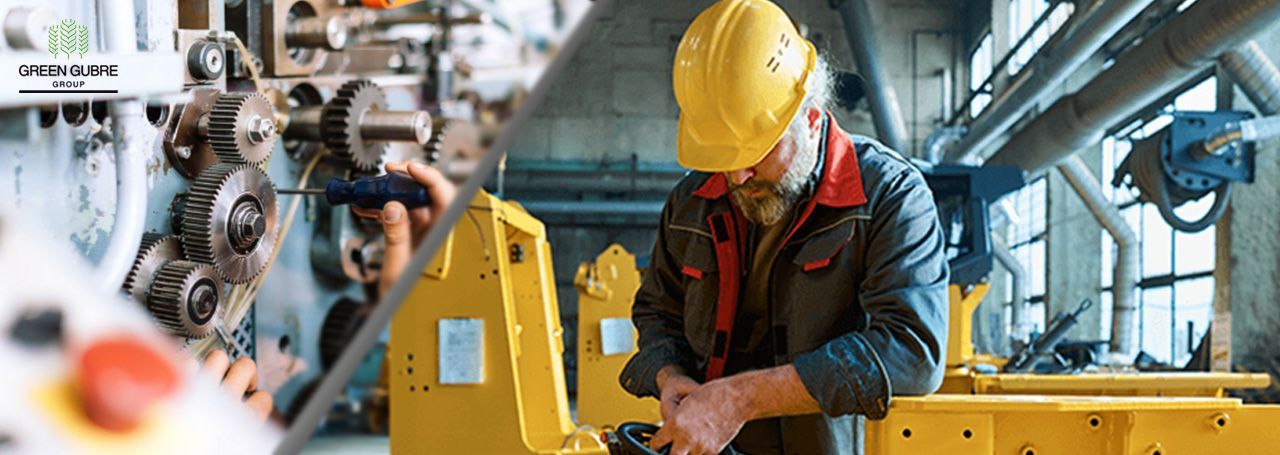
Regular maintenance of industrial equipment is crucial for ensuring the smooth operation, longevity, and safety of machinery. In industries such as manufacturing, mining, construction, and energy production, the performance of equipment directly impacts productivity and profitability. This blog delves into the importance of scheduled maintenance, its benefits, and how implementing a maintenance program can save costs and prevent downtime.
Why Industrial Equipment Maintenance Matters:
Industrial equipment is exposed to heavy wear and tear, environmental factors, and high operational loads. Without regular maintenance, even the most durable machines are prone to failure, which can lead to costly repairs, unscheduled downtime, and safety hazards. Maintenance programs are designed to minimize these risks by addressing issues before they escalate. Moreover, well-maintained equipment operates more efficiently, reducing energy consumption and improving overall productivity.
Key Benefits of Regular Maintenance for Industrial Equipment:
1. Extended Equipment Lifespan:
Regular maintenance ensures that industrial equipment runs smoothly for a longer period. By identifying and repairing wear-and-tear issues early, maintenance prevents minor problems from becoming major breakdowns that could shorten the lifespan of the machinery. Proper lubrication, calibration, and inspection help keep all components in optimal condition, extending the equipment’s useful life.
2. Improved Safety:
Faulty machinery can pose significant safety hazards to workers and the facility. Regular maintenance checks help identify potential risks, such as malfunctioning parts, leaks, or electrical issues, before they lead to accidents. Well-maintained equipment ensures a safer working environment, which is especially important in industries like construction and manufacturing, where safety is a top priority.
3. Reduced Downtime and Increased Productivity:
Equipment breakdowns can cause unplanned downtime, leading to delays in production schedules and reduced output. Regular maintenance helps prevent unexpected breakdowns by ensuring that machines are operating efficiently and reliably. By minimizing downtime, companies can maintain consistent production levels, meet deadlines, and increase overall productivity.
4. Cost Savings on Repairs:
Preventive maintenance is far more cost-effective than reactive repairs. When equipment is regularly inspected and maintained, small issues can be addressed before they evolve into major problems that require expensive repairs or even full equipment replacement. Investing in regular maintenance reduces the need for costly emergency repairs and helps avoid the financial burden of purchasing new machinery.
5. Energy Efficiency and Environmental Benefits:
Well-maintained equipment operates more efficiently, consuming less energy during operation. For example, properly lubricated machinery reduces friction, allowing it to function smoothly and with less energy. This not only leads to cost savings but also reduces the environmental impact by lowering the facility’s energy consumption. In addition, efficient equipment produces fewer emissions, contributing to more environmentally friendly industrial practices.
Types of Maintenance for Industrial Equipment:
1. Preventive Maintenance:
Preventive maintenance involves scheduled inspections, cleaning, lubrication, and repairs to prevent equipment failure. This approach ensures that machinery is running optimally and addresses issues before they become serious. Common preventive maintenance tasks include checking for wear on moving parts, replacing filters, and lubricating components.
2. Predictive Maintenance:
Predictive maintenance uses advanced monitoring tools to assess the condition of machinery and predict when it is likely to fail. Technologies such as vibration analysis, infrared thermography, and oil analysis are used to monitor equipment health and identify early signs of deterioration. Predictive maintenance helps optimize maintenance schedules, allowing for repairs to be made just in time before a breakdown occurs.
3. Corrective Maintenance:
Corrective maintenance involves repairing or replacing parts after a fault has been detected. This type of maintenance is reactive, addressing issues as they arise. While it is often more costly than preventive or predictive maintenance, corrective maintenance is necessary when a breakdown occurs and immediate repairs are required.
4. Condition-Based Maintenance:
Condition-based maintenance monitors the real-time condition of equipment and triggers maintenance activities only when specific thresholds or conditions are met. This method uses sensors and data analytics to provide real-time insights into the equipment’s health, allowing maintenance to be performed only when necessary. It is a cost-effective approach that ensures machinery is maintained based on actual operating conditions rather than a fixed schedule.
Steps for Implementing a Maintenance Program:
1. Assess Equipment Needs:
Start by evaluating the specific maintenance needs of each piece of equipment in your facility. Consider factors such as operational load, frequency of use, and the environment in which the machinery operates. Some equipment may require more frequent maintenance than others based on these factors.
2. Create a Maintenance Schedule:
Develop a maintenance schedule that outlines when each machine should be inspected, cleaned, and serviced. Preventive maintenance tasks should be performed at regular intervals, while predictive or condition-based maintenance can be scheduled based on data from monitoring tools.
3. Train Personnel:
Ensure that maintenance staff and operators are properly trained in performing maintenance tasks and identifying signs of equipment failure. Regular training helps workers understand the importance of maintenance and empowers them to take proactive steps to maintain equipment.
4. Use Monitoring Tools:
Implement monitoring tools and sensors to track the condition of critical equipment. These tools provide real-time data on temperature, vibration, and other key performance indicators that can signal when maintenance is needed.
5. Keep Detailed Records:
Maintain detailed records of all maintenance activities, including inspections, repairs, and part replacements. These records help track the history of each machine, making it easier to identify patterns of wear and predict future maintenance needs.
Common Industrial Equipment Maintenance Tasks:
1. Lubrication:
Proper lubrication is essential for reducing friction between moving parts, preventing wear and tear, and ensuring smooth operation. Regular lubrication also prevents overheating and extends the life of components.
2. Calibration:
Many types of industrial equipment require precise calibration to function correctly. Regular calibration ensures that the machinery operates within the correct parameters, preventing errors and ensuring product quality.
3. Filter Replacement:
Filters are commonly used in industrial machinery to remove contaminants from air, oil, or hydraulic fluids. Regular filter replacement is necessary to maintain the efficiency of the equipment and prevent contamination-related issues.
4. Inspection of Electrical Components:
Electrical systems are critical to the operation of many types of industrial machinery. Regular inspection of wiring, connections, and control panels helps prevent electrical failures and reduces the risk of short circuits or fires.
5. Cleaning and Debris Removal:
Industrial equipment often accumulates dust, dirt, and debris during operation. Regular cleaning prevents blockages, overheating, and other issues that can result from a buildup of contaminants.
Conclusion:
Regular maintenance of industrial equipment is essential for optimizing performance, reducing downtime, and ensuring safety in the workplace. By implementing a well-structured maintenance program, industries can extend the lifespan of their equipment, improve energy efficiency, and reduce costs associated with repairs and replacements. Whether through preventive, predictive, or condition-based maintenance, taking proactive steps to care for machinery leads to improved productivity and profitability.