The Role of Tool Steel in Manufacturing High-Performance Tools
The Role of Tool Steel in Manufacturing High-Performance Tools
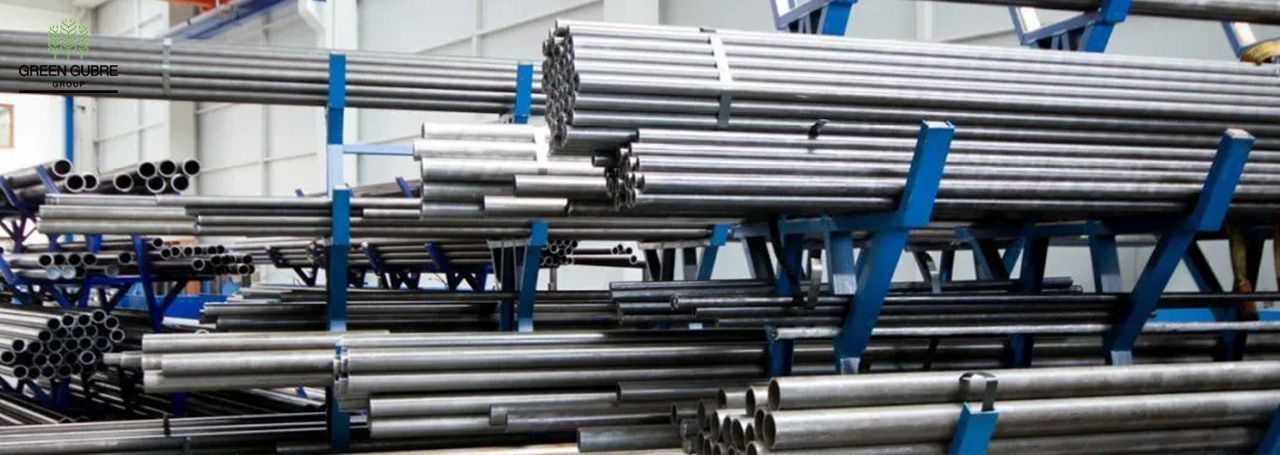
Tool steel is a vital material used in the manufacturing of high-performance tools and machinery parts that must withstand extreme conditions such as high temperatures, abrasion, and wear. Known for its hardness, toughness, and heat resistance, tool steel is used in applications ranging from cutting tools and dies to molds and industrial machinery. This blog explores the various types of tool steel, their properties, and their significance in industrial manufacturing processes.
What is
Tool Steel?
Tool steel is a type of carbon and alloy steel that is specifically designed to produce tools that are used for cutting, shaping, and forming materials. Its composition includes a combination of elements like tungsten, molybdenum, chromium, vanadium, and cobalt, which give the steel unique properties such as high hardness, wear resistance, and the ability to retain shape under high temperatures.
Types of Tool Steel:
1. Water-Hardening Tool Steel (W-Grades):
- This is the most basic form of tool steel and is known for its low cost and high wear resistance.
- Used in applications such as cutting tools, chisels, and punches that require hardness but operate at low temperatures.
2. Cold-Work Tool Steel (O, A, D-Grades):
- Designed for cutting and shaping at room temperature, cold-work tool steels are extremely hard and wear-resistant.
- Commonly used in dies, shear blades, and cutting tools for industrial applications.
3. Hot-Work Tool Steel (H-Grades):
- These steels are designed to retain their strength and hardness at high temperatures, making them ideal for hot-forging, die-casting, and extrusion tools.
- Known for excellent toughness, hot-work tool steels are used in molds for casting and forging.
4. High-Speed Tool Steel (T, M-Grades):
- High-speed tool steel is designed for high-performance tools that need to operate at high speeds without losing their hardness.
- Used in the production of drills, milling cutters, and other cutting tools that experience extreme heat and wear during operation.
5. Shock-Resistant Tool Steel (S-Grades):
- Specifically engineered to absorb impact and resist shock, this type of tool steel is used in tools like hammers, chisels, and punches.
- It is designed to handle sudden impacts without breaking or chipping.
Key Benefits of Tool Steel:
1. Hardness and Wear Resistance:
Tool steel is known for its exceptional hardness, which allows it to cut and shape other materials effectively. This hardness also ensures excellent wear resistance, meaning that tools made from tool steel last longer and maintain their sharpness even after extensive use.
2. Heat Resistance:
Tool steel can withstand high temperatures without losing its structural integrity, making it ideal for applications where heat exposure is constant, such as in forging and die-casting tools.
3. Toughness and Impact Resistance:
Many types of tool steel are designed to be tough, allowing them to absorb impact and resist chipping or breaking during heavy-duty applications. This toughness is critical in tools like punches and hammers that experience sudden force.
4. Dimensional Stability:
Tool steel retains its shape and size even after repeated exposure to high temperatures and stress. This stability is crucial for precision tools used in manufacturing, where maintaining exact dimensions is essential for product quality.
Applications of Tool Steel:
1. Cutting Tools:
Tool steel is extensively used in the manufacturing of cutting tools such as drills, saw blades, milling cutters, and lathe tools. High-speed steel (HSS) is particularly valuable in this application due to its ability to maintain hardness at high cutting speeds.
2. Molds and Dies:
Hot-work tool steels are commonly used to manufacture molds and dies for casting, forging, and extrusion processes. These tools need to endure high temperatures and wear while maintaining dimensional accuracy, making tool steel the ideal material.
3. Punches and Chisels:
Shock-resistant tool steel is used to produce punches, chisels, and other tools that need to absorb impact without breaking or deforming. This property is especially important in heavy-duty applications like metal forming and fabrication.
4. Industrial Machinery:
Tool steel is also used in various components of industrial machinery that require high strength, toughness, and resistance to wear. This includes machine parts, gears, and fixtures that are subject to extreme conditions during manufacturing operations.
5. Automotive and Aerospace Industries:
In both the automotive and aerospace sectors, tool steel is used in the production of components that must withstand high temperatures and stresses, such as engine parts, turbines, and transmission components.
Grades of Tool Steel:
- W-Grades (Water-Hardening): Cost-effective with high hardness but limited to low-temperature applications.
- O, A, D-Grades (Cold-Work): Superior wear resistance for tools used in cold environments.
- H-Grades (Hot-Work): Excellent for tools exposed to high temperatures and thermal cycling.
- T, M-Grades (High-Speed): Ideal for tools that operate at high cutting speeds, offering hardness retention at elevated temperatures.
- S-Grades (Shock-Resistant): Built to absorb impact and prevent breaking under sudden forces.
Global Demand for Tool Steel:
The demand for tool steel is growing globally due to its wide range of applications in industries such as manufacturing, automotive, aerospace, and construction. As industries continue to innovate and develop new technologies, the need for durable, heat-resistant, and wear-resistant materials like tool steel is becoming more prominent. Additionally, the growing trend toward automation in manufacturing processes has further driven the demand for precision tools made from high-quality tool steel.
Sustainability and Recyclability
Tool steel is a highly recyclable material, making it a sustainable choice for manufacturers looking to reduce waste and environmental impact. The durability and long service life of tools made from tool steel also contribute to sustainability by reducing the need for frequent replacements.
Conclusion
Tool steel is an essential material in modern manufacturing, providing the hardness, toughness, and heat resistance needed for high-performance tools. From cutting and shaping materials to forming and molding components, tool steel plays a crucial role in ensuring the efficiency and longevity of industrial processes. As demand for durable, high-performance tools continues to rise across various industries, tool steel will remain at the forefront of innovation and production. Explore our range of tool steel products designed to meet the needs of your specific applications on our dedicated product page.