Exploring the Benefits of High-Speed Steel in Modern Manufacturing
Exploring the Benefits of High-Speed Steel in Modern Manufacturing
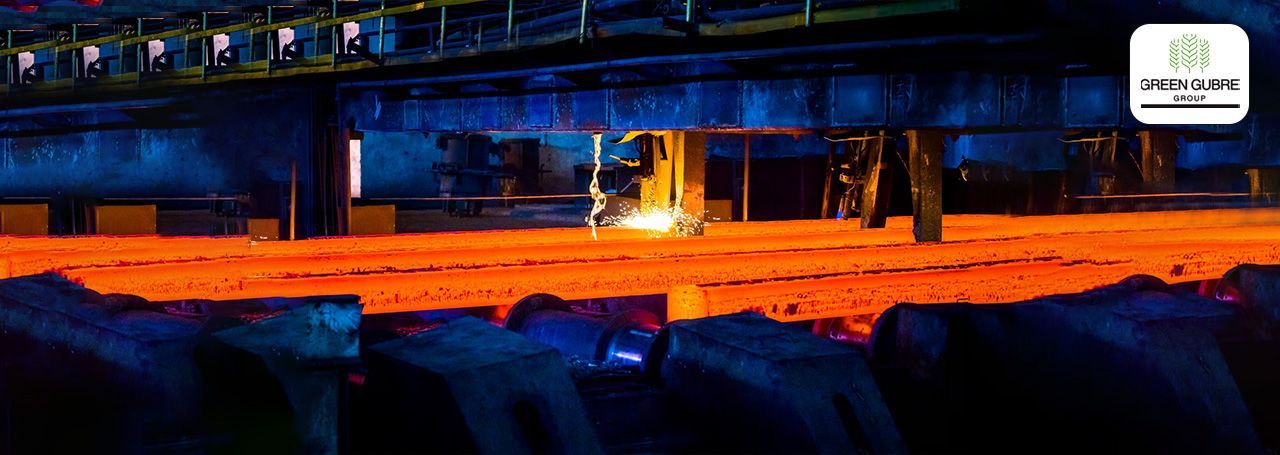
High-speed steel (HSS) is a premium-grade tool steel renowned for its exceptional hardness, heat resistance, and ability to maintain sharpness under high-temperature conditions. HSS is widely used in manufacturing industries that require cutting tools capable of performing at high speeds without losing performance. This blog explores the properties, advantages, and applications of high-speed steel in modern manufacturing, highlighting its significance in industries such as automotive, aerospace, and tool production.
What is
High-Speed Steel?
High-speed steel is a type of tool steel that contains a blend of carbon, tungsten, molybdenum, chromium, and vanadium. This alloying process gives HSS its unique ability to withstand extreme heat generated during high-speed machining operations, making it ideal for use in cutting tools, drills, saw blades, and milling cutters. The superior hardness and heat resistance of HSS enables it to maintain its edge sharpness and performance, even when exposed to temperatures as high as 600°C (1112°F).
Key Properties of
High-Speed Steel:
1. Heat Resistance:
High-speed steel retains its hardness and cutting ability even at elevated temperatures, making it suitable for high-speed cutting applications where heat build-up is inevitable.
2. Wear Resistance:
HSS has exceptional wear resistance, allowing it to maintain sharp edges and high performance over long periods of use. This reduces the need for frequent tool changes, increasing productivity in machining processes.
3. Toughness and Durability:
High-speed steel is known for its toughness and durability, enabling it to withstand the stress of cutting, drilling, and milling at high speeds. It resists chipping and breakage, ensuring long-lasting performance.
4. Hardness:
The hardness of high-speed steel, achieved through alloying and heat treatment, allows it to cut through tough materials such as stainless steel, titanium, and hardened alloys. This makes it indispensable for precision machining and high-stress applications.
Benefits of
High-Speed Steel:
1. Increased Productivity:
High-speed steel allows for faster cutting speeds in manufacturing processes, reducing cycle times and increasing productivity. Its ability to retain sharpness and hardness at high temperatures ensures continuous performance in demanding conditions.
2. Cost-Effective Performance:
While HSS tools may have a higher initial cost compared to carbon steel tools, their long-lasting performance and reduced need for re-sharpening make them a cost-effective choice over time. The durability of HSS tools minimizes downtime and maintenance costs in industrial settings.
3. Precision and Accuracy:
HSS cutting tools provide precise and accurate cuts, making them ideal for applications that require fine tolerances and high-quality finishes. This precision is essential in industries such as aerospace and automotive manufacturing, where accuracy is critical.
4. Versatility:
High-speed steel is versatile and can be used to manufacture a wide range of cutting tools, including drill bits, taps, reamers, end mills, and saw blades. Its adaptability makes it suitable for various machining operations, from rough cutting to precision finishing.
Applications of
High-Speed Steel:
1. Cutting Tools:
High-speed steel is primarily used to manufacture cutting tools that can withstand high-speed operations without losing their cutting edge. These tools include drill bits, lathe tools, milling cutters, and taps, all of which benefit from the hardness and heat resistance of HSS.
2. Automotive Industry:
In the automotive industry, high-speed steel tools are used for machining engine components, transmission parts, and other critical components that require precision and durability. The ability of HSS to cut through tough materials like hardened steel makes it indispensable in automotive manufacturing.
3. Aerospace Industry:
The aerospace industry relies on high-speed steel for the precision machining of turbine blades, aircraft components, and engine parts. The heat resistance and toughness of HSS ensure reliable performance in high-temperature environments and high-stress applications.
4. Metalworking:
High-speed steel is widely used in metalworking applications where cutting, drilling, and milling of metal materials are required. Its ability to maintain sharpness under continuous use makes it a preferred choice for machining steel, aluminum, and other metals.
5. Tool and Die Making:
Tool and die manufacturers use high-speed steel to produce dies, punches, and molds that require exceptional hardness and wear resistance. HSS tools can handle the high pressures and repeated use involved in metal stamping, forging, and extrusion processes.
Types of
High-Speed Steel:
1. M Series (Molybdenum-Based):
The M series of high-speed steel is characterized by its molybdenum content, which enhances its toughness and resistance to softening at high temperatures. This type of HSS is commonly used for general-purpose cutting tools, such as drills and taps.
2. T Series (Tungsten-Based):
The T series of high-speed steel contains tungsten, which provides excellent hardness and heat resistance. T series HSS is preferred for applications that require cutting through hard materials at very high speeds, such as in heavy-duty milling and turning operations.
3. Cobalt-High-Speed Steel:
Cobalt-added high-speed steel offers improved heat resistance and hardness, making it suitable for cutting extremely tough materials like stainless steel and nickel-based alloys. Cobalt HSS is often used in high-performance drills and end mills.
Global Demand for
High-Speed Steel:
The demand for high-speed steel is growing globally, driven by the increasing need for high-performance cutting tools in manufacturing industries. The automotive, aerospace, and metalworking sectors are key contributors to the demand for HSS tools, as they require materials that can handle high-speed machining and extreme operating conditions. Additionally, as manufacturers seek to improve efficiency and reduce costs, the durability and longevity of high-speed steel tools are becoming increasingly attractive.
Sustainability and Recyclability:
High-speed steel is a sustainable material, as it can be recycled and reused in various forms. The recycling of HSS tools reduces waste and contributes to the sustainability goals of manufacturing industries. Additionally, the long lifespan of HSS tools minimizes the need for frequent replacements, reducing the consumption of raw materials and energy in tool production.
Conclusion:
High-speed steel is a critical material in modern manufacturing, offering exceptional hardness, heat resistance, and durability for high-performance cutting tools. Its versatility and ability to maintain sharpness at high speeds make it an indispensable material in industries that require precision machining and high-speed operations. From automotive and aerospace to metalworking and tool production, high-speed steel plays a vital role in improving productivity and ensuring the quality of manufactured products. Explore our range of high-quality high-speed steel products designed for superior performance in demanding applications by visiting our dedicated product page.